What to Know Before Beginning to Weld
Welding is both an art and a science, and it plays a crucial role in numerous industries, from construction and manufacturing to automotive and aerospace. With advancements like robotic welding transforming the field, it's essential to equip yourself with the right knowledge and skills to ensure safety and quality in your projects. This blog post outlines key aspects to consider before embarking on your welding journey, helping you to lay a solid foundation for both learning and practice.
Understand the Different Types of Welding
There are several types of welding methods, each suited for specific materials and applications. Among the most common types are MIG, TIG, and Arc welding. MIG (Metal Inert Gas) welding is often considered the easiest for beginners, as it uses a wire electrode and requires minimal setup. TIG (Tungsten Inert Gas) welding offers greater precision but demands more skill. According to Monroe, arc welding, one of the most popular methods, is usually performed with an arc temperature of roughly 10,000 degrees Fahrenheit. Additionally, robotic welding is becoming increasingly prevalent for its efficiency and consistency in industrial applications. Understanding these differences will help you choose the best starting point for your projects.
Invest in Quality Safety Equipment
Welding can be hazardous without the proper safety equipment. High temperatures, intense light, and flying sparks pose significant risks, making it imperative to invest in quality safety gear. Essential equipment includes a welding mask with a proper shade to protect your eyes from harmful ultraviolet and infrared light emissions. Additionally, use fire-resistant clothing, gloves, and sturdy footwear to mitigate burns and injuries associated with welding. For those working with robotic welding systems, ensuring proper safety protocols around automated machinery is equally important. Prioritizing safety not only shields you from harm but also promotes confidence and focus in your work, helping to maintain productivity and prevent costly accidents.
Focus on Proper Training and Certification
Before beginning any welding projects, seek out formal training and, if possible, obtain a certification. Many community colleges and trade schools offer comprehensive welding programs that cover the basics and advanced techniques you’ll need. These programs often include theoretical studies as well as practical sessions, giving you hands-on experience under mentored supervision. Some programs also introduce students to robotic welding, which is increasingly important in modern manufacturing. Earning a certification not only enhances your skills but also boosts your credibility within the industry, potentially opening doors to more advanced opportunities down the line.
Learn to Maintain Your Equipment
Welding equipment is an investment, and proper maintenance is crucial to ensure its longevity and performance. Familiarize yourself with the routine checks and servicing required for your welding machine, whether it’s a MIG, TIG, or Arc welder. For those using robotic welding systems, regular calibration and software updates are also essential to maintain precision. Keeping your equipment in optimal condition not only extends its life but also enhances safety and effectiveness during use. Simple practices such as regular cleaning, inspecting cables and connections, and replacing worn parts can prevent accidents and costly repairs, ensuring consistent, high-quality welds every time.
Understand the Importance of Material Preparation
Proper material preparation is critical to a successful weld. This involves cleaning the surfaces to remove contaminants such as rust, oil, and dirt, which can weaken the weld and lead to failures. Additionally, understanding the properties of the metal you're working with, such as thickness and composition, helps you tailor your welding approach. In robotic welding, precise material preparation is especially important to ensure consistent, high-quality results. Material preparation not only affects the strength of the weld but also its appearance, making it an essential step for professional-looking results.
Embarking on a welding journey requires a blend of theoretical knowledge, practical skills, and an unwavering commitment to safety. By understanding different welding types—including advancements like robotic welding—investing in quality safety gear, seeking proper training, maintaining equipment, and emphasizing material preparation, you set the stage for a successful foray into this versatile craft. As you advance, the knowledge and skills you acquire will become invaluable tools, empowering you to undertake a wide range of projects with confidence and precision.
Ready to take your welding projects to the next level? Contact Ray-Mac, Inc today to learn how our expertise in robotic welding can deliver precision, efficiency, and unmatched quality for your industrial needs.
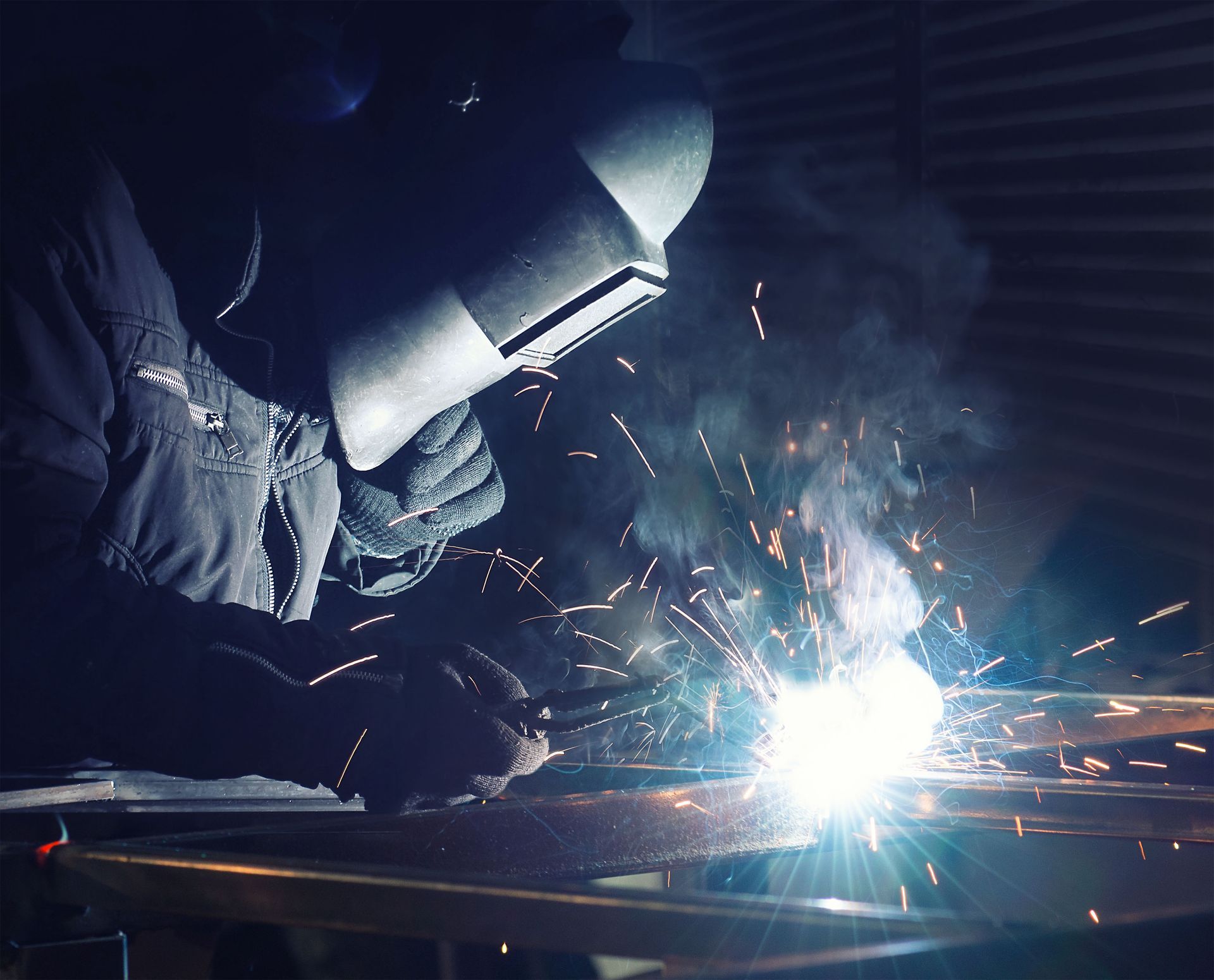
Share On: